All you need to know about induction furnaces
An induction furnace is an electric furnace in which heat is applied through induction heating which is simply a method of transferring heat energy. Induction furnaces are ideal for melting and alloying a wide variety of metals like iron and steel, copper, aluminum, and even precious metals with minimum metal losses. The capacities of these furnaces range from less than one kilogram to one hundred tons. The greatest advantage of induction furnaces is that they are clean, well-controllable, and energy efficient as compared to most other means of melting metals.
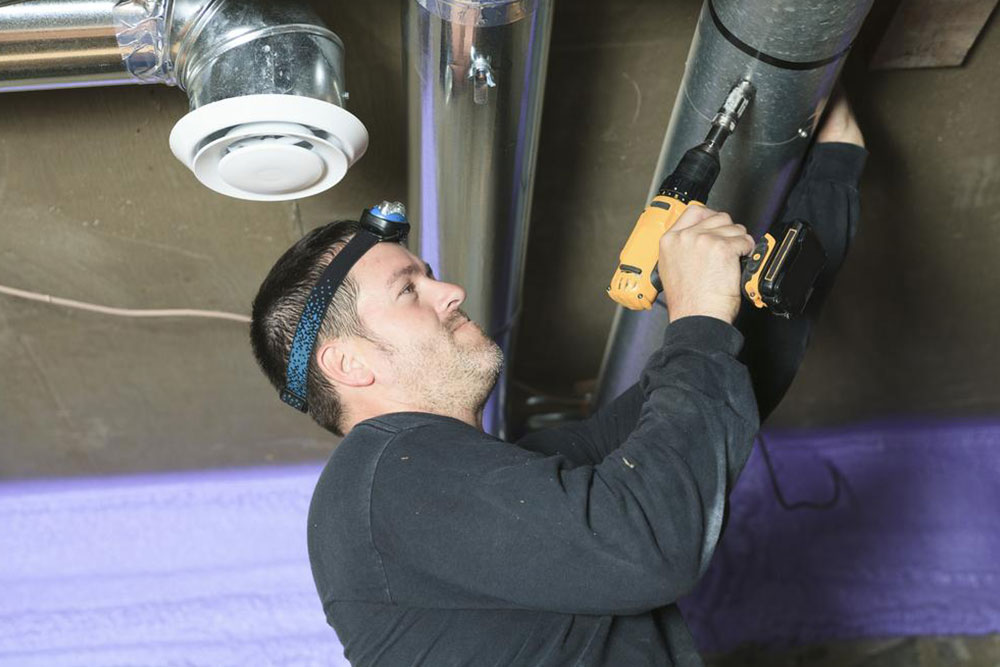
Most modern foundries use an induction furnace. Nowadays, even most iron foundries are replacing cupolas with induction furnaces to cast iron, as the former emits lots of dust and other pollutants. The only major drawback of using induction furnaces in foundries is the lack of refining capacity and that some alloying elements may be lost due to oxidation.
There are two main types of induction furnaces. They have been explained in brief as follows:
- Coreless induction furnaces: The heart of this type of furnace is the coil, which comprises a hollow section of high conductivity copper tubing which is wound into a helical coil. The coreless induction furnace has largely replaced the crucible furnace, especially for the melting of high melting-point alloys. It is commonly used to melt all grades of steel and iron, as well as many non-ferrous alloys.
- Channel induction furnaces: They consist of a refractory-lined steel shell that contains the molten metal. Channel induction furnaces are commonly used for melting low melting-point alloys and as a super-heating unit for higher melting-point alloys, such as cast iron. Channel induction furnaces can also be used as holders for metal melted off-peak in coreless induction furnace units, thereby reducing total metal costs by avoiding peak demand charges.
The advantages of using an induction furnace can be listed as follows:
- Optimized consistency
- Maximized productivity
- Improved product quality
- Extended fixture life
- Environmentally sound
- Reduced energy consumption
Disclaimer:
The content provided on our blog site traverses numerous categories, offering readers valuable and practical information. Readers can use the editorial team’s research and data to gain more insights into their topics of interest. However, they are requested not to treat the articles as conclusive. The website team cannot be held responsible for differences in data or inaccuracies found across other platforms. Please also note that the site might also miss out on various schemes and offers available that the readers may find more beneficial than the ones we cover.