Things you should know about tubeless tires
There were attempts in England and South Africa to manufacture tubeless tires in the thirties and forties. In England, a patent was granted to one Killen Tire in 1930. Wingfoot Corporation, a subsidiary of Goodyear in South Africa, got a patent in 1944. Both these companies could not make use of the patent as they encountered technical difficulties, which they could not overcome. After limited production, manufacturing was, however, discontinued.
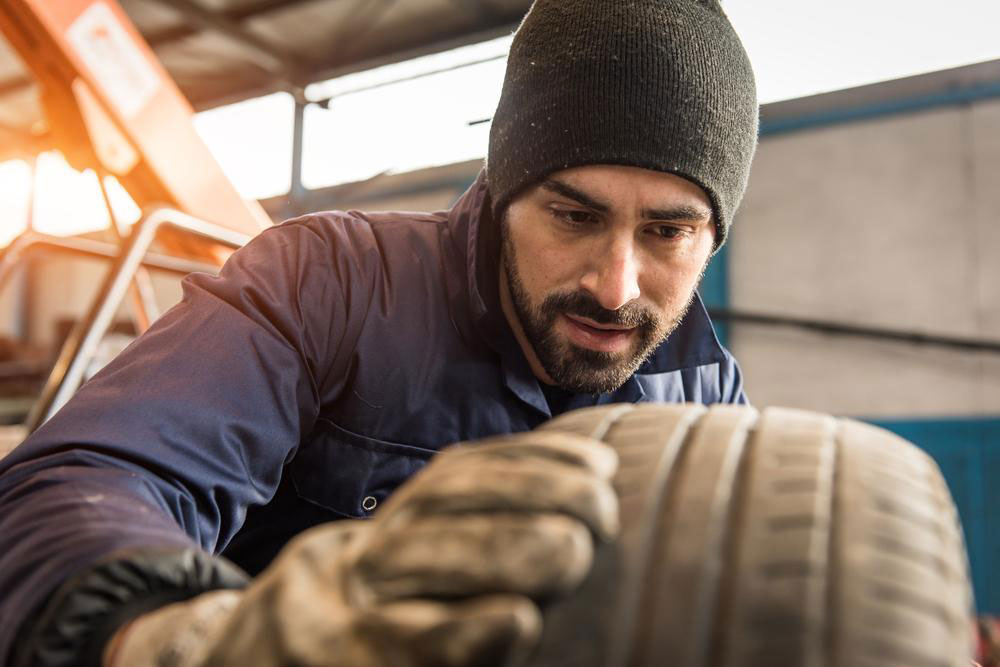
The traditional tire had a thin walled tube inside the rubber casing called the carcass. The air filling nozzle with a self-sealing valve is mounted on the tube. This design has a few inherent limitations. When the tire is rolling there is a relative motion in between the tube and the wall which varies with air pressure in the tube and the speed. Lower pressure than design results in an increased friction and consequential heating up. This is very significant in nonstop long-distance runs. This, in turn, increases the air pressure which can be considerable. This can cause an over pressure burst with catastrophic results. The second is that in the case of a puncture air will leak from the tube, initially through puncture hole on the tube. This leaded air would normally leak out through the imperfection on the carcassrim seating and also through the passage for the valve tube on the rim. As the pressure in the tube decreases the tube contracts and the valve tube gets pulled in leading to a rapid depressurization and a catastrophic blowout.
In the tubeless tire, a perfect sealing is achieved between the beads of the carcass and the rim. The beads have integrally molded ridges which press and seal with the rim when the tire is inflated. The butyl rubber lining limits the permeability of air and also reduces the air leak through the puncture. Advantages of the tubeless tire over the conventional are scarcely a rapid depressurization and blow out, higher mileage, more comfortable ride and better cornering characteristics. Tubeless tires have become the standard fitting in most countries.